Objective:
To provide ASIC managers with a guideline to
allocate the time, personnel and materials necessary to deliver ASIC
flight parts on schedule and within budget.
The magnitude and complexity of ASIC programs for space
applications demand careful planning and judicious use of resources.
We encourage you to invest the necessary time in this primary task.
Throughout your planning process remember that the reliability,
radiation and testing requirements unique to producing space parts
will influence all segments of your planning. Also, pay particular
attention to the four major bottlenecks
encountered in an ASIC program: simulation (verification), test
vector generation, system integration (evaluation in a system
environment), and part screening. Comprehensive planning of
resources helps eliminate ad hoc solutions and ensures a smooth flow
of the program.
To develop the most cost effective and time efficient use of
resources, build your plan around each of the major ASIC tasks set
forth in the first chapter of this section. The tasks are: set
requirements, ASIC trade-offs, vendor selection, partitioning, ASIC
implementation, physical layout, manufacturing, test and
characterization, and part acceptance.
The following is a list of steps to follow when
assembling a management plan for ASIC activities:
- First develop a time schedule for arriving at each milestone.
- Identify the responsible parties for each milestone.
- Examine which stages depend upon the progress of another stage.
We will present schedules for the following high-level ASIC tasks, each broken into a number of sub-tasks:
- ASIC vendor evaluation
- ASIC design
- ASIC fabrication
- ASIC part acceptance
We then present a schedule of major ASIC activity synthesized from
those used in ASIC programs for the Cassini mission at JPL. Gleaning
from all this information and considering his group's experience in
various aspects of ASIC work, the ASIC manager can then synthesize
his or her own ASIC schedules.
As discussed in Chapter 1 of this section, we recommend completing
the ASIC vendor evaluation after determining the initial
requirements for all ASICs in a project or system. (See Table 1.2.1).
Table 1.2.1 ASIC Vendor Evaluation
The time for ASIC design activity varies, depending upon the design
team's experience in ASIC design and in particular technologies, such
as the type of cell library, type of process, etc. Design activity time
also depends upon design complexity along with other requirements,
such as testability and performance. A few rules of thumb will help
guide you through this decision-making process. Plan for 3k to 5k
gates per person, per month when doing a gate-level design. The
numbers vary widely when using synthesis tools. It appears that
gate-level synthesis does not yet shorten design time, unless there is
a system-wide commitment to the identical synthesis tools and the
approach. However, gate-level synthesis may increase reliability
when done correctly, thus improving other aspects of the design
process. (See Table 1.2.2).
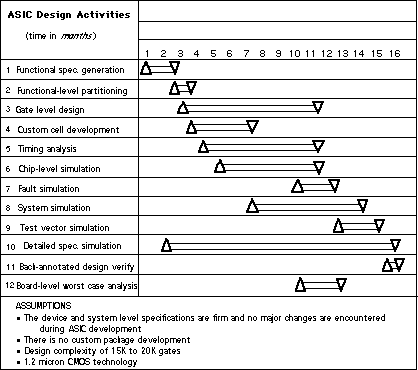
Table 1.2.2 ASIC Design
Using standard cells versus gate arrays will generally have major
differences for the following reasons:
- The design process normally takes longer to complete, since the
standard cell approach is often undertaken with some custom cell
development in mind. Low to moderate complexity custom cells may
take four to eight weeks of additional time.
- Floor planning, physical layout and back annotated layout
verification would take three to five weeks longer than a gate array
schedule.
To make sure you meet your ASIC time schedule, we recommend
that you tie the vendor to a fabrication schedule by including it in
the ASIC contract. We strongly advise that negotiations consider the
time schedule as well as cost. For example, a gain in the fabrication
time schedule may justify the increased cost of using a "hot
lot" option--ASIC wafer lots given priority in a fabrication
facility--especially when problems have delayed the work
elsewhere. Check the vendor's flexibility to accommodate such
needs. (See Table 1.2.3).
Table 1.2.3 ASIC Fabrication
Part acceptance depends heavily on the requirements of your
project. If the project requires full QPL or QML devices, then part
acceptance is relatively fixed. The only major exceptions relate to
whether or not the space-specific appendix of the QML specification
is invoked.
Remember, part acceptance activity calls for reviewing data from
testing and screening to determine the device's suitability for a
particular application. This means the part should not only meet the
required functionality and performance but also show evidence of
reliability in the intended application. (See Table 1.2.4).
Table 1.2.4 ASIC Part Acceptance
Equipment and tools take extensive planning for space ASICs. As the
complexity of a device increases, so does the need for equipment and
tools to ensure the parts meet the requirements. Commercial ASICs
do not undergo the radiation and reliability tests required of a space
flight part, making equipment and tool planning a simpler process.
Off-the shelf parts require less testing, and therefore less equipment
and fewer tools, because data already exists on the parts. The next
section, Vendor Evaluation, describes the selection process for
equipment and tools in detail.
An inventory of tools and equipment will tell you what you need to
buy. However, before purchasing consider the ever changing market
of equipment. When counting on available tools or equipment, the
time factor becomes critical. Make sure the equipment will be
available within your required time frame; simulators, testers or any
other resources may be put in place but they may be tied up when
you need to use them.
Consider all aspects of the ASIC program to determine any overlap.
Carefully look at design, test, manufacturing, failure analysis,
characterization, and screening, before purchasing new hardware and
tools in the following areas:
- mainframes
- workstations
- PCs
- hardware accelerators
- logic modeling devices
- testers (engineering and production)
- plotters
- communication devices (modems etc. to talk to vendor)
- hardware (in-circuit) emulation devices
- ESD evaluators
Take care not to over buy equipment such as workstations and CAE
tools; they are evolving so fast that they only have a typical lifetime
of three to four years. Consider future upgrades and keep
maintenance in mind when preparing a budget for tools and
platforms.
Also, the choice of design methodology has great implications on
workstations, design capture, and verification tools. Because of the
tremendous number of variations from vendor to vendor, we cannot
discuss the trade-offs of buying bundled or unbundled tools with
platforms. We suggest managers analyze needs to determine the
best packages for your ASIC work.
Workstations, mainframes, and PCs with tools installed from one or
more CAE companies may be used for the following tasks:
- schematic capture
- synthesis/compilation
- timing verification
- simulation
- single chip simulation
- multi-chip simulation
- behavioral simulation
- mixed-mode simulation (when analog and digital are mixed on
the same chip)
- simulation accelerators
- SPICE-level simulation
- fault grading
- test synthesis
- floor planning
- physical layout
- hardware emulation of ASIC logic
- die size estimation
- translators (from one platform or tool to other)
- FPGAs (used for protyping) to gate array/standard cell designs
- cost estimation
- concurrent engineering tools
- porting of any part of third party libraries
- design alternative analysis
- ATPG tools
- IDDQ vector generation and translation tools
- thermal and power analysis tools
- quick prototyping tools
For manufacturing, test, failure analysis
(F/A), characterization, and screening consider the following:
- testers (functional, parametric, AC (at speed), IDDQ)
- burn-in chambers
- mechanical inspection
- thermal analysis
- access to FA/QA labs (subcontracting if services not available
within your organization)
In the above list, we have covered tools and equipment for all
possible aspects of an ASIC program. A particular program may only
require a subset of these lists. Check that tools are portable and
interoperable before purchase. Also check for standardization.
When using a vendor's megacells, make sure the vendor's standard
tool set supports them and that this tool set is used in-house. Some
vendors may only support megacells through their design centers.
Contracting with a third party to do ASIC designs can relieve many of
these tool responsibilities at the cost of creating and sticking with an
excellent ASIC device specification.
The unique nature of ASICs makes it imperative that you find
personnel with the appropriate skills for the task; generally this
means they must have experience with ASICs. For example, a team
responsible for commercial ASIC design must have logic design and
design simulation methodology skills. For space ASICs, a design team
must also be cognizant of the radiation, reliability, and testability
aspects of designing for the rigorous requirements a space part must
meet. Specification writing, design verification, physical layout, the
chip sign-off process, and ASIC verification at the system-level are
also skills an ASIC team must possess.
INTERNAL PERSONNEL
"The ASIC management team needs to develop a working
partnership with numerous groups and with several disciplines
within NASA."
The heart of a successful ASIC is design. We recommend that
designers have the following qualifications:
- board-level design experience
- diverse electronic design skills including simulation, design
analysis, and design verification skills
- ability to make justifiable and rational trade-offs between
extended design verification activity and schedule constraints
- ability to communicate with groups from diverse professional
backgrounds
The magnitude and complexity of the ASICs will dictate the number
of designers needed. Determining just how much one person can
accomplish often proves a skill in itself. As discussed earlier, a few
rules of thumb will help guide you through this decision-making
process. Plan for 3k to 5k gates per person, per month when doing a
gate level design. This number can vary depending upon the
complexity of a design, familiarity with tools, and skill level of
designers.
The following suggestions may help in planning:
- Take into account the learning curve for new tools.
- Identify tools that will require a lot of technical support. These
typically are new types of tools. An example would be synthesis
tools for design and test.
- Anticipate the special requirements of large designs. Choose tools
and approaches that support multiple designers working on the same
device and/or platform
- Maintain consistency between teams when designing a system
with multiple ASICs.
- Identify one person to manage design libraries and communicate
with the vendor on CAE and CAT issues when a project calls for
multiple ASICs with the same vendor. For example, if you plan to
use a Joint Test Action Group (JTAG) boundary scan approach for all
ASICs, assign one designer who understands the scan chain, its
description, its incorporation into tools, and silicon, etc. The assigned
designer will communicate with the vendor and with all of the ASIC
designers about boundary scan work.
As an ASIC manager, you should get to know a number of groups and
be ready to take advantage their expertise. A list of these groups
and their associated ASIC support capabilities follows:
ASIC Center/Parts/Component Engineering Group:
- helps make ASIC trade-offs, and assists in evaluating technology,
tools, and vendors
- provides ongoing support to work with the vendor
- advises ASIC manager on procurement support issues
- provides test vector generation, translation of test vectors into
different formats, part qualification, characterization, and screening
(overall reliability) support
- Participates in the chip sign-off process
CAE/CAT Group:
- obtains libraries from the vendor
- integrates libraries onto your choice of platforms
- maintains these libraries through configuration management
practices
- coordinates verification and maintenance of any custom cell
- installs, maintains, and offers training for tools
- performs stuck-at fault analysis (fault grading)
- may write any translators required to convert data from one
platform or tester format to another
- involved heavily in the chip sign-off process
Procurement and Legal Group:
- supports the generation and negotiation of a complete ASIC
contract
- guides and supports the generation of an SOW
- supports vendor evaluation and vendor selection
- provides support during the execution of the general contract
Failure Analysis Group:
You may find these services available within your organization. If
they are not available, plan these services through an outside group
or the vendor. Many NASA projects contractually require failure
analysis capability to minimize the impact of failures. Failure
analysis support includes:
- determining causes of ASIC failures
- recommending ways to avoid future failures
Documentation Group:
Besides the groups described above, during various reviews you will
likely work with groups such as an architecture group, a system-
level implementation group, and a software development group.
A close working partnership usually develops between the vendor
and various groups of your organization. As an ASIC manager, it is in
your best interest to manage these relationships. You need to
establish clearly the various points of contact, the task
responsibilities, change and configuration control and other aspects
of the relationship between your company and the vendor.
Otherwise, there exists a real chance of the ASIC vendor receiving
incorrect data and conflicting direction.
Producing ASICs for NASA introduces a new set of considerations for
calculating budget expenditures. Even though you may be familiar
with producing commercial ASICs, you will find that costing space
ASICs differs enormously. Again radiation and reliability testing
represent the major differences in budget. Commercial ASICs simply
don't undergo this testing; commercial testing is included in design
non-recurring engineering (NRE) charges or per piece pricing. When
using off-the-shelf parts the vendor performs the radiation testing;
design/process reliability has already been established.
As a manager of an ASIC program, you need to know where budget
overruns commonly occur. Managers often overlook the cost of tools
for discrete verification. They also may underestimate the NRE cost
because they don't understand the elaborate testing costs. QML and
QPL impose stringent test characteristics on the vendor, which the
commercial producer does not have to abide by.
We will look at each of these individually to illustrate the cost
characteristics unique to space ASICs.
TOOLS
The ASIC vendor's ability to supply as complete a solution as possible
is the first point to consider about tools. Closely coupled with this is
tool maturity. You do not want to pay for the debug of a set of tools
new to an ASIC vendor with your engineers, your schedule, and your
dollars.
As you evaluate your potential ASIC vendors (see Section Two), keep in mind the
costs of sticking with any existing CAD tools you may already have;
forcing the ASIC vendor's cell library and tools to work with them
will almost always cost more in the long run than starting over with
one of the ASIC vendor-supported CAD toolsets. Unfortunately, at
present such miracle cures as design compilers for this classic
problem, which may work for translating cell libraries from one CAD
toolset to another, don't translate vendor tool functions at all.
As a rule of thumb, minimize the number of vendors needed to
design and build your ASIC. Each vendor brings a new set of
learning curves, maintenance, and new interfaces, all representing
more costs and time. Since a mature ASIC vendor will have already
done many designs with their in-house toolset, they are the first
place to look for tools.
Remember, the design of an ASIC is one of the most challenging
management of complexity problems engineers face. The choice of
CAD toolset can help solve this problem or make it much worse.
PERSONNEL
"Costing space ASICs differs enormously from costing
commercial ASICs."
Be careful not to underestimate the cost of personnel and support
groups essential to producing space ASICs. They will consume a
considerable portion of your budget. Take into account personnel
that you may have to pay for, both on your ASIC team and from
other parts of your organization, who perform or support the
following:
- making ASIC trade-offs
- evaluating and selecting tools, an ASIC technology, and a vendor
- procurement
- design
- design verification
- test generation
- library, tool, and vendor support
- part characterization, screening, and part acceptance
- failure analysis
- documentation
- program management
VENDORS
The vendors will have some fixed and some variable costs. NRE
charges represent fixed costs, which usually include physical layout
and mask making charges. NRE also includes a limited number of
prototype devices and limited central processing unit (CPU) time for
any post-layout verification. Variable costs associated with
engineering and flight parts will obviously depend upon the quantity
requirements. You should consider the additional cost of having a
vendor do any special custom macro design, custom package
development, or test and characterization. Also consider anything
that goes beyond their standard procedures, such as going through a
place and route more than once, additional CPU time used on the
vendor's mainframe, faster fabrication, and packaging services.
ASIC designers create the test vectors required for the chip sign-off
process. Creating IDDQ test vectors may require
translation from your workstation format to the vendor's format and
from the vendor's tester format to a NASA center's tester format.
These translations can result in significant cost.
Quality assurance, characterization, and screening are major cost
components in the high reliability NASA arena. We identified
support function costs from the personnel point of view previously.
Some of these functions may be performed in part or jointly by the
vendor, a NASA center internal parts group, or a third party.
The ASIC manager should allocate extra development costs to allow
for the possibility that the program may incur one or more of the
following: a second pass silicon; development of a new base array
and its characterization; application specific tools; and doing a third
party design as applicable.
The following graphic contains a schedule synthesized from
schedules created for a number of ASICs fabricated for the Cassini
mission at JPL. They follow the assumptions set forth in the tables
regarding vendor evaluation, design, fabrication, and part acceptance
at the beginning of this chapter.
These schedules represent the first ASICs that JPL has done with a
vendor. They also represent the first ASICs for most of the designers
involved. As such, they reflect a typical first time ASIC schedule for
any organization.
Note: JPL noted that the IDDQ work in items 54 through
61 of the following schedule detected significantly more defects than
stuck-at fault testing. At this time, however, it is not clear how to
quantify the reliability risks these defects represent. As a result of
this and similar work, it is possible that IDDQ testing may
replace some or all stuck-at fault testing.
Summary
- Identify all ASIC tasks and allocate sufficient resources to
complete them.
- Line-up the resources available from the ASIC center, parts
specialists, procurement, and other groups in your organization
early.
- Line-up early all of the resources (some free and some not)
available from the ASIC vendor.
- Carefully consider ASIC tool resources and the way they
influence:
- ASIC vendor selection
- efficient design partitioning
- thorough design verification
- ASIC part reliability
- obsolete tool replacement
- ASIC design group efficiency/training needs
- If ASICs are new to your organization make sure you have the
resources needed for training personnel, including:
- designers
- procurement personnel
- part specialists
- quality assurance personnel
- Time, as a resource proves difficult to manage in an ASIC
program. Formal reviews, both within and outside the organization,
are strong motivators. Plan for them carefully and utilize them to
the fullest.
Now you may jump to: